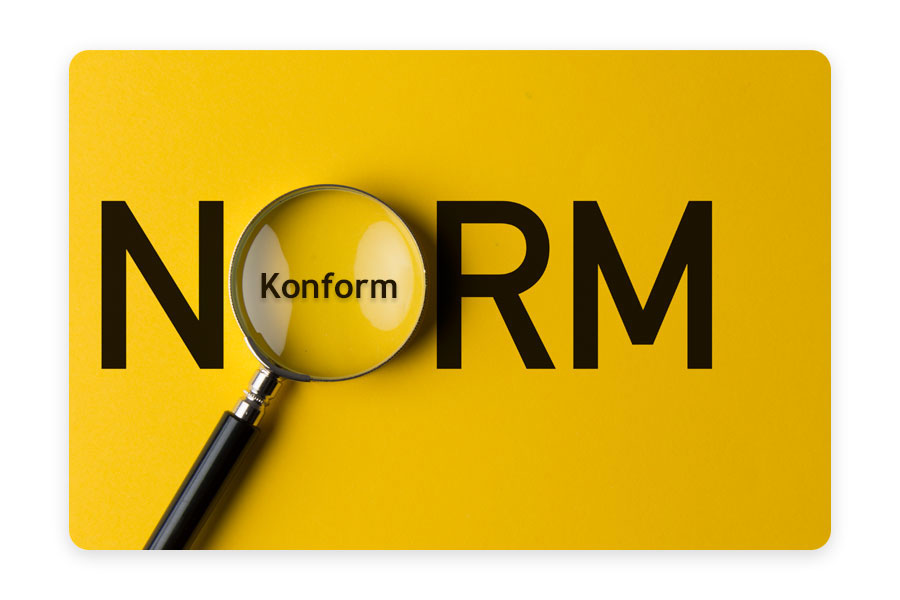
Unser Leistungsspektrum
Mit der CE-Kennzeichnung erklärt ein Hersteller gegenüber den Marktaufsichtsbehörden, dass ein Produkt mit allen anzuwendenden Rechtsvorschriften konform ist, welche eine Anbringung des CE-Zeichens vorsehen
- Erstellung von Risikobeurteilungen
- Erstellung von Betriebanleitungen
- Beratungsleistungen für Ihr Produkt / Ihre Anlage
- Produkt definieren
- Richtline ermitteln
- Normen ermitteln und anwenden
- Benannte Stelle
- Konformitätsbewertungsverfahren durchführen
- Erstellung technischer Unterlagen
- EG-Konformitätserklärung verfassen und CE-Kennzeichen anbringen
Leistungsspektrum Beratung Lean
Lean Production Methoden fokussieren traditionell die kontinuierliche Verbesserung (KAIZEN). Viele Lean Methoden richten sich daher logischerweise auf das Entdecken von Verschwendung in bestehenden Prozessen. So stoßen sie den kontinuierlichen Verbesserungsprozess im Unternehmen immer wieder neu an.
Mit unseren gut ausgebildeten Mitarbeitern und umfangreichen digitalen Tools unterstützen wir Sie bei der Prozessoptimierung in Ihrer Produktion. Dabei wenden wir nicht nur auf gängige Lean Production Methoden an, sondern sind auch Ihr starker Partner bei der Umsetzung der Ergebnisse – ob bei der Anpassung Ihrer Prozesse oder sinnvolle der Implementierung von Technologien.
Um Ihnen einen tieferen Einblick zu verschaffen, wie Waitkus bei Prozessoptimierungen vorgehen, stellen wir Ihnen nachfolgend einige Lean Production Methoden vor:
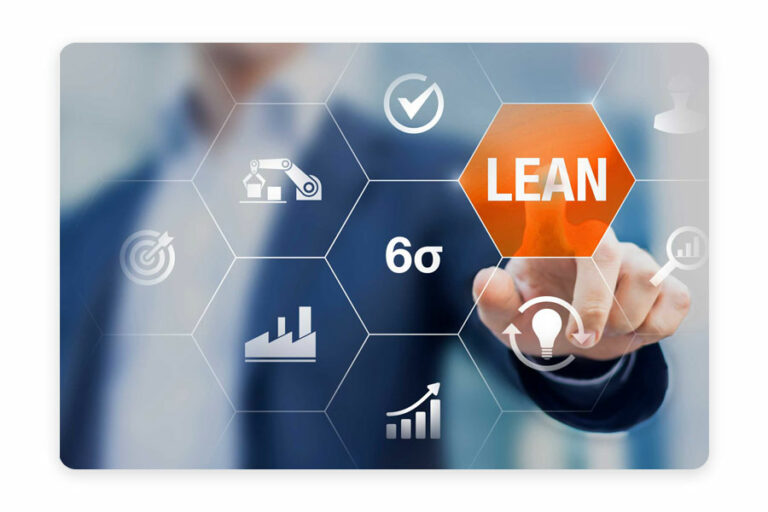
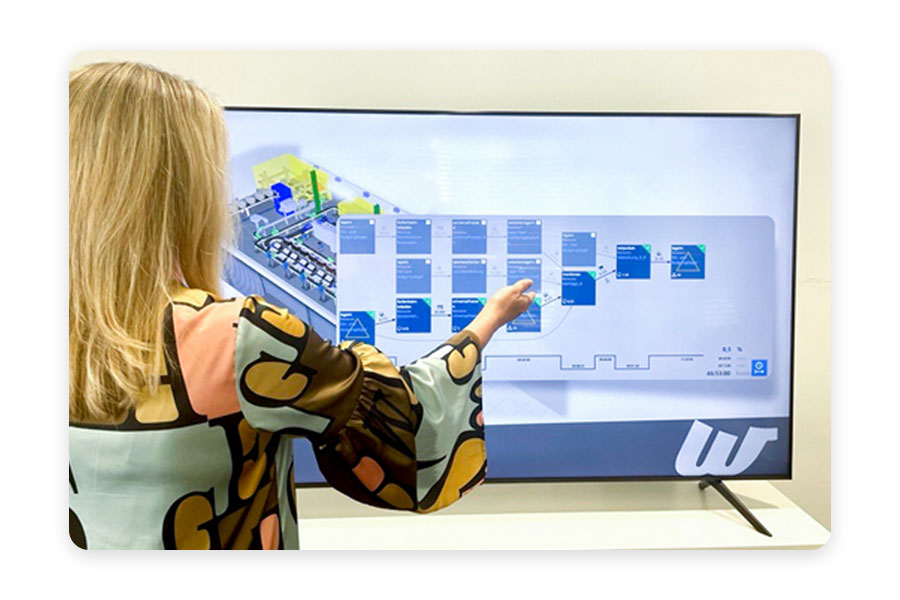
Methode 1: Wertstrom
Als Wertstrom bezeichnet man im Lean Management mit leicht pathetischer Überhöhung den Warenstrom vom Lieferanten bis zum Kunden. Der Begriff unterstellt, dass dem Materialfluss besondere Beachtung zu schenken ist, weil Material nicht nur wertvoll ist, sondern von Prozessschritt zu Prozessschritt Ressourcen hineingesteckt werden, wodurch es theoretisch immer wertvoller wird. Am Ende muss dieser Wert jedoch vom Kunden honoriert werden, wobei man davon ausgehen darf, dass der Kunde nur wirklich wertsteigernde Prozessschritte belohnt. In dieser einfachen Logik begründet sich das gesamte Konzept der Lean Production, die alles nicht wertsteigernde als Verschwendung deklariert und zu eliminieren versucht.
Für die Planung so schlanker Prozesse hat sich das Wertstromdesign in der Praxis durchgesetzt. Hierbei wird zuerst diejenige Produktfamilie in den Fokus genommen, die für das Unternehmen das größte Gewinnpotenzial darstellt. Häufig orientiert man sich hierzu am Umsatzanteil. Für diese Produktfamilie wird ein Kundenverbrauchstakt definiert. Gemeint ist damit ein fiktiver Rhythmus, in dem der Kunde die in der Produktfamilie zusammengefassten Produktvarianten im Mittel kontinuierlich benötigt und abnimmt. Nun gestaltet man alle Prozessschritte im Fluss so, dass sie ihren Output im Kundentakt abgeben können. Damit wird dem Aufstauen von Puffermengen zwischen den Prozessschritten entgegengewirkt, der Umlaufbestand des wertvollen Materials liegt dadurch im Minimum. Alle versorgenden Prozesse (Nebenflüsse) müssen sich unterordnen. Im Prinzip führt Wertstromdesign also auf einen getakteten Fließprozess.
Der Charme dieser Lean Methode liegt darin, dass der Gesamtzusammenhang aus Materialfluss und dessen Steuerung auf einem Blatt Papier dargestellt wird. Dabei sind allen Best-practice-Bausteinen der Lean Production Symbole zugewiesen, woraus die praktische Umsetzung in der Produktion erkennbar ist. So sind z. B. notwendige Supermärkte und KANBAN-Regelkreise sowie die in den Prozessschritten notwendigen Personalstärken direkt aus der Wertstrom-Darstellung abzulesen. Für die Fabrikplanung entsteht damit eine leicht verständliche Gestaltungsvorlage für die im Layout einzuplanenden Produktions- und Logistiksysteme sowie ihre Verkettung.
Methode 2: KANBAN
Das Wort Kanban entstammt dem Japanischen. Dort bezeichnet der Begriff eine Karte, ein Schild bzw. einen Beleg. Als Methode der Lean Production erlangte KANBAN i. V. m. dem Toyota Produktionssystem Bedeutung, was durch einige viel beachtete Veröffentlichungen beginnend in den 1990er Jahren zu einer breiten Wahrnehmung im Management nahezu aller produzierenden Unternehmen führte. Die Historie dieser Methode geht sogar bis in die 1950er Jahre zurück. Später setzte sie der japanische Ingenieur Taiichi Ohno zur Steuerung des Materialflusses bei Toyota systematisch ein. Ziel von KANBAN ist die Begrenzung des Umlaufbestandes auf ein Mindestmaß. Denn Bestand gilt im Lean Management als Verschwendungsart, weil er Kapital und Raum bindet, ohne dass dadurch Wertzuwachs entsteht.
Das Wirkungsprinzip von KANBAN ist einfach: Jedem KANBAN wird eine feste Materialmenge zugewiesen und die Anzahl der zirkulierenden KANBANs in Form von Informationsträgern oder Behältern fixiert. Die technische Umsetzung reicht vom simplen Zwei-Behälter-Prinzip bis zu ausgeklügelten elektronisch unterstützten Steuerungen i. V. mit Nivellierungsstrategien für die variantenreiche Serienfertigung; Stichwort EPEI. Der Input dafür entstammt dem Soll-Wertstrom, wo mit der Taktung auch die Abruffrequenz für sämtliche Materialien festgelegt wird.
Nun mag man der Methode berechtigt Steuerungscharakter zuschreiben, für die Fabrikplanung ist KANBAN dennoch wesentlich. Denn durch KANBAN-Regelkreise wird zum einen die Transportintensität und zum anderen der Platzbedarf für Umlaufbestände determiniert. Beide Größen benötigt man bereits beim Entwurf der Produktionsstruktur. Hierzu müssen Flächenzuschläge für Materialbereitstellung z. B. für ein Blocklayout dimensioniert und alle resultierenden Flächen entsprechend der zu- und abgehenden Materialfluss-Intensitäten zueinander flussgerecht angeordnet werden.
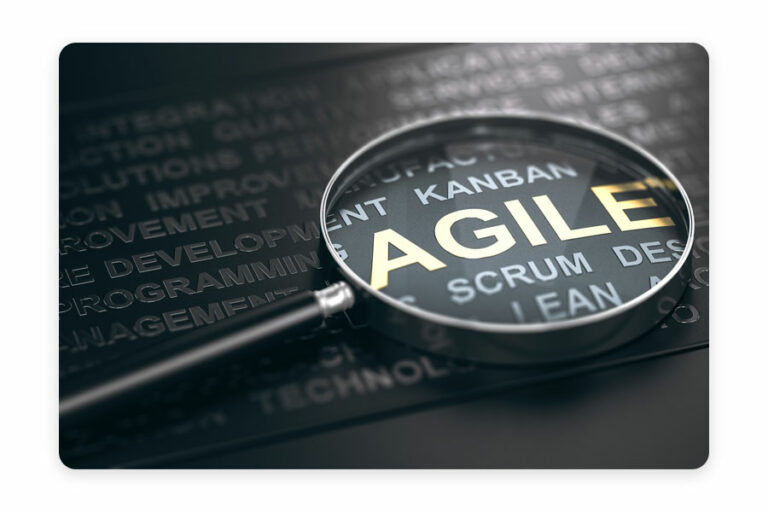
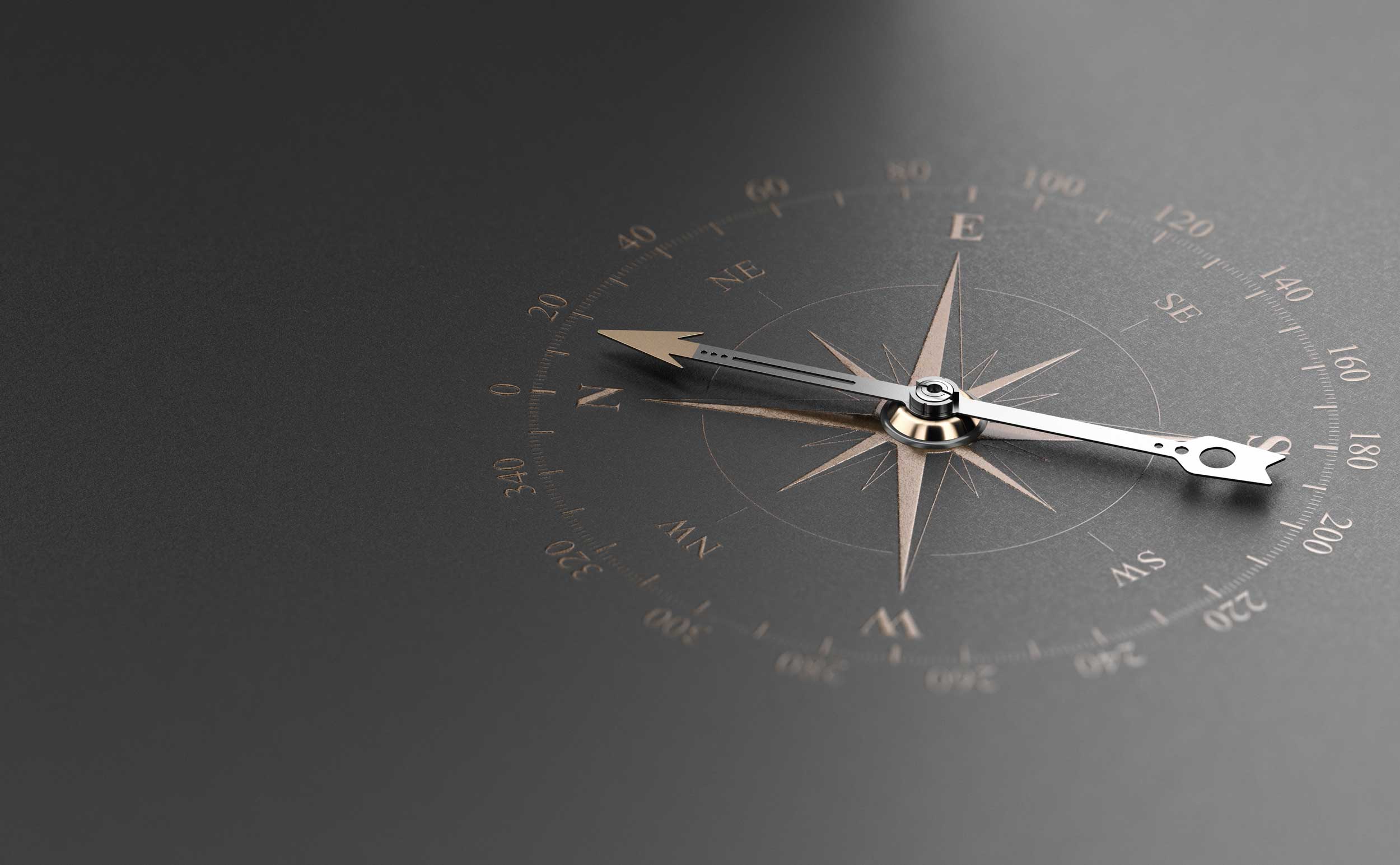
Methode 3: Cardboard Engineering
Cardboard Engineering ist Lean Thinking in Reinform. Denn hierbei wird auf simpelste Art mit einfachsten Mitteln Wertschöpfung gestaltet. Das Einbeziehen der Betroffenen ist ein wesentlicher Erfolgsfaktor der Methode. Im Kern werden dazu auf Basis von Erfahrung und dem Prinzip der Best-Point-Bereitstellung Arbeitsplätze in Pappe oder Holzkonstruktionen umgesetzt, um darauf erste Arbeitsversuche zu unternehmen. Der gesamte Prozess wird von denjenigen vollzogen, die später diese Arbeitsplätze nutzen sollen. Das Ganze wird als Workshop umgesetzt, in dessen Ergebnis die prototypischen Arbeitsplätze i. d. R. mit Industrieprofilen oder Steckrohr-Systemen realisiert werden.
Für die Fabrikplanung ist dieses Konzept wertvoll, weil es Mitarbeiterinnen und Mitarbeiter in die Gestaltung der Arbeitsplätze einbezieht. Damit wird vor allem die Akzeptanz erhöht, wenn effiziente Lean-Lösungen umzusetzen sind. Zudem nimmt man den Betroffenen damit die Angst vor nachteiligen Veränderungen. Denn schlanke Produktion wird oft mit Leistungsdruck in Verbindung gebracht, weil man zu Unrecht unterstellt, dass mehr Output nur durch mehr Einsatz erreichbar wäre. Dabei zeigen gerade erst die konstruktiven Feebacks der Mitarbeiterinnen und Mitarbeiter die im Detail schlummernden Verschwendungen in neu entwickelten Prozessen auf.
Methode 4: Spagetti–Diagramm
Dieses Werkzeug gehört zu den bekanntesten Lean-Instrumenten. Für Fabrikplaner erzeugt es insbesondere für Feinlayouts von Arbeitsbereichen wertvollen Input, um die Materialbereitstellung zu gestalten. Denn die Spaghetti-Linien, die zur Darstellung der Laufwege ganz klassisch lean auf einem Blatt Papier in ein ausgedrucktes Layout gezeichnet werden, liefern dem Layoutplaner die zur Anordnungsoptimierung benötigten Transportintensitäten.
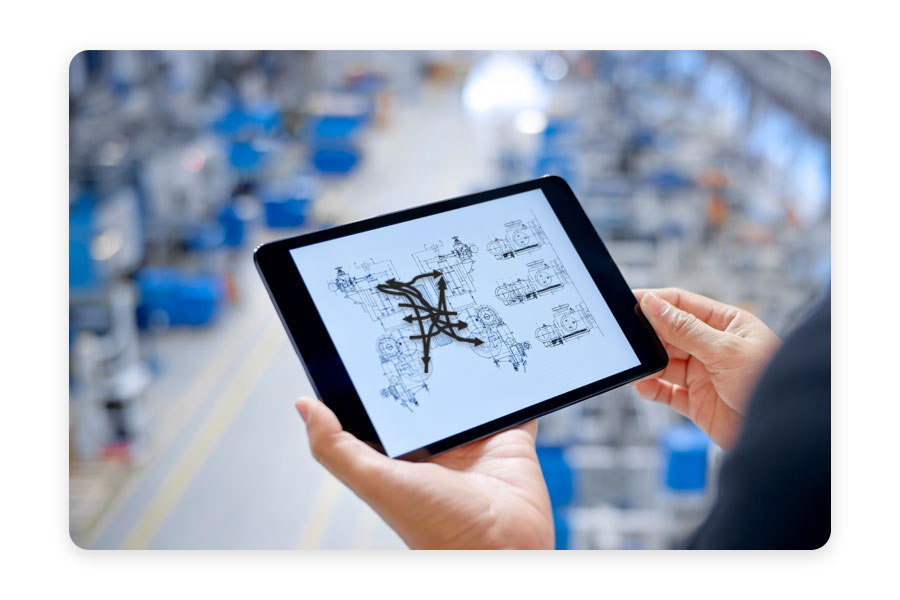
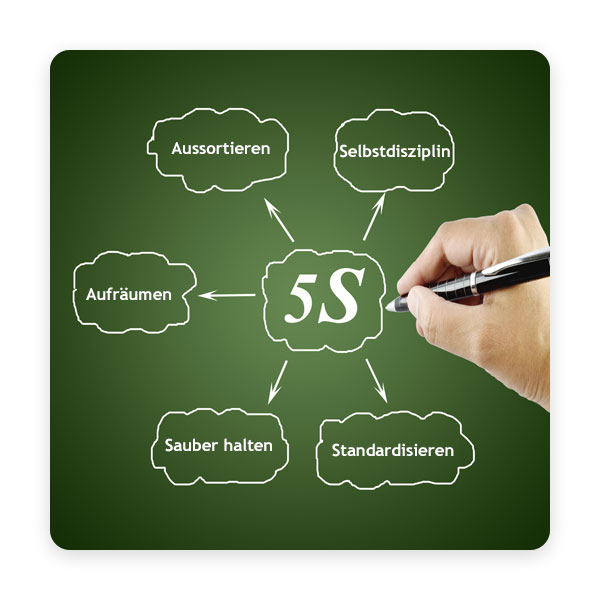
Methode 5: Die 5 "S"
Mit den fünf „S“ sind im Lean Management die dem Japanischen entstammenden Begriffe
- Seiri (Aussortieren)
- Seiton (Aufräumen)
- Seiso (Sauber halten)
- Seiketsu (Standardisieren)
- Shitsuke (Selbstdisziplin)
Gut umgesetzt ist 5 S nämlich ein Kristallisationskern für Best-practice-Standards. Hieraus entstehen z. B. Arbeitsplatz-Lösungen, die aufgrund ihrer gleichartigen Gestaltung ein leichtes Einarbeiten unterschiedlicher Mitarbeiterinnen und Mitarbeiter ermöglichen. So sind gleiche Werkzeuge immer am selben Ort aufbewahrt, es gibt Standards für die Normteilebereitstellung u. a. hilfreiche Festlegungen, die zu modularen Gestaltungslösungen führen. All dies vereinfacht Planungsprozesse. Denn modulare Systeme erlauben das mehrfache Nutzen von einmal entworfenen 3D-Modellen. Die Planungsgeschwindigkeit steigt, da weniger oft nach neuen konstruktiven Lösungen gesucht werden muss. Vorteile hat das ebenfalls für die Dimensionierung von Flächenbedarfen. Denn bewährte Ist-Anordnungen können direkt in neue Layouts übernommen werden.
Voraussetzung für gute Standards ist jedoch, dass sie tatsächlich auch lean sind. Aus diesem Grund ist das erste „S“ dem Aussortieren gewidmet. Ziel ist, dass alle Dinge, die nicht häufig benutzt werden müssen, sich gar nicht erst in den Standard einschleichen. In der Lean-Praxis wird hierzu gern die Rote-Karte-Aktion genutzt: Alle Dinge, die man als überflüssig einschätzt, erhalten eine rote Markierung (z. B. als Klebepunkt). Wenn dann in einem Zeitraum von z. B. einem Tag diese Dinge tatsächlich nicht benutzt werden, erhalten sie einen Platz außerhalb des Arbeitsbereichs. So entstehen sukzessive Zonen klassifiziert nach Nutzungshäufigkeit. Schnell wird klar, was wirklich gebraucht wird und damit auch, was den Lean-Standard für den betrachteten Bereich im Unternehmen bilden sollte.
Fazit:
Diese fünf Methoden aus dem Lean Production bieten uns die Chance, Ihre Produktivität zu steigern. Denn unser Ziel ist es, in Ihren Produktionsumgebung identifizierte Quellen für Verschwendung durch Planungsstandards auszuräumen und ein nachhaltiger KAIZEN in Ihrem Produktion erhalten.